Friday, December 18, 2009
Attribute R3_SA_ORG with value (abbr. of sales org) already assigned to O (object ID number)
Message no. 5AT123
Diagnosis:
The attribute R3_SA_ORG can only be used with a specified value once at any particular time.
The value (Abbr. of sales org) was already assigned to object O (Object Id number).
Solution:
Reason u get this error is because you are trying to assign sales org of ECC or R/3 to organization created in BP in CRM manually but while importing sales org data from ECC or R/3 Organization in CRM is automatically created which means you jus have to delete the organization assigned instead assign the org that is shown in error.
Error during RFC connection to OLPT system
Diagnosis
The connection to the connected OLTP R/3 System could not be created.
System Response
The data from the R/3 system cannot be read and transferred.
Procedure
Check whether an R/3 system is connected. You find these settings in Customizing for Customer Relationship Management under CRM Middleware and Related Components -> Communication Settings -> Set Up Logical Systems.
Solution: Follow the link below.
https://cw.sdn.sap.com/cw/docs/DOC-29530%3bsaplb_*=(J2EE8941820)8941850
Thursday, December 17, 2009
General /Organizational units/Master Data
• Name the relevant organizational units for SD and explain how they are used?
• What is a Company code in the R/3 system?
• Does SD master data have to be maintained at company code level?
• What is a Sales organization in R/3 system?
• What is Distribution channel in R/3 system?
• Which organizational units combine to make up a sales area?
• What does the material type control?
• What is determined by specifying an industry sector?
• Does SD master data have to be maintained at company code level?
• Which material master view is valid for all clients?
• To sell a material, which views do you have to maintain in the material master data?
• What do the partner functions do in the customer master record?
• Which Organizational units do you have to enter when creating a sales order? Do you have to maintain the customer or material master records for all of these units?
• We have 4 sales area and 2 company codes. The customer can buy from both sales areas. How many customer numbers would this customer leave?
• What is an account group?
Sales
• How is a sales document structured?
• How can you differentiate between individual sales document types?
• What does the sales item category control?
• What is a rush order?
• What is a Cash Order?
• How do you use a scheduling agreement?
• Which functions enable you to copy data from one document to another in SD?
• What is an incompletion procedure in SD?
• How can you display preceding and subsequent documents for a certain documents?
Pricing
• What is a condition record?
• What is an access sequence?
• What is a pricing procedure and how is it determined?
• What is particular about header conditions?
• What are group conditions? What is the purpose in a group condition?
• What do you know about manual pricing changes?
• How are statistical conditions flagged?
• What are conditions supplements?
• Can condition records be created with reference to an existing condition?
• To create price changes you must create a new condition record?
• Can Condition records be created by copying an existing condition record?
• Copy rule controls the copying of condition records?
• Your organization has its own pricing condition type and linked to their condition tables. They would like to maintain the records from a central area. How can they accomplish this?
• We need to provide a customer with prices for a selected group of materials. What tool does SAP provide us to accomplish this?
• How can we create condition record that will not be used in the price determination but to be used for planning purposes in CO-PA?
• How can SAP handle multiple levels of a Customer or Product Hierarchy in one condition record?
Shipping
• Name the functions in the shipping process.
• What conditions must be met before you can combine several sales order items in one delivery?
• What must you do if you want to pack the materials that are to be delivered?
• What is a shipping point? What factors are important when it is determined?
• What is a transportation planning point? Which organizational units is it assigned to?
• Before you can deliver an order, What Prerequisites do you have to meet?
• What do you know about picking deliveries?
• What do you trigger by posting goods issue in the R/3 system?
• What is delivery scheduling?
• How is the item category for an item Category?
• What does a deliver type control?
• What does a delivery item Category control?
• How are item categories in the delivery determined?
• When determined the delivery date what scheduling is taken into account to arrive at the delivery date?
• When does the system switch to forward scheduling to determine the delivery date?
• If you are not using the transportation component and your organization wants to maintain the shipping related nditions (e.g. postal charges) what tools are available in SAP?
Transportation
• What factors influence the automatic route determination?
• Who can you create a shipment?
• What does transportation planning do?
• What is particular about the shipment cost document?
• What prerequisite must be met before the shipment costs can be settled?
• How can you transfer shipment costs to Financial Accounting?
Billing related questions
• Which data is updated when you create a billing document?
• In the standard system, accounting determination is dependent on certain factors. What are they?
• How is pricing determined?
• What are the factors that influence Pricing?
• What is the billing date and how is it determined?
• What is a rebate agreement? What are the prerequisites for rebate processing?
• How do you define rebate agreements and how is the rebate amount calculated?
• With reference to which document types Credit and debit memos are created in the R/3 standard system?
• Which data can you change in the billing document once it has been transferred to financial Accounting?
• What is a billing plan in the R/3 system?
• A billing transaction can be blocked by setting a billing block in what documents and at what level.
• SAP provides a tool to perform collective billing, what documents can be created using this tool?
• What is account determination based upon?
• What does billing document update in CO-PA?
Basic Packing process
Repeat for the material to be packed. In our case Material MTS
1) Create Packing Instructions (it is like a formula definition -that how you want to pack your material) in
T-code-POP1.
2) Packing determination in T-code - POF1.
T-code - VL01N Outbound Delivery -> Packing Enter the materials at top and at bottom (Select Material - MTS and Edit - Pack). This is how the basic process of packing works.
Wednesday, December 16, 2009
Automatic creation of BP (business partner) at PPOMA_CRM
Go to the following IMG path: Customer Relationship Management -> Master Data -> Business Partner -> Integration Business Partner-Organization Management -> Set Up Integration with Organizational Management.
Find the entries starting with HRALX. You should have those entries:
• HRLAX - HRAC with the value ‘X', if you don't create this entry in the table and Save.
Group Sem.abbr. Value abbr. Discription
HRALX HRAC X Activate HR Integration
• HRLAX-OBPON with the value ‘ON', if you don't create this entry in the table and Save.
The system did not find a valid bill of material, Message no. V1113
Diagnosis: The system tried to find a bill of material for the material entered, taking into account material MTS, plant CR16, date 15.12.2009 and BOM usage SD01.
However, no bill of material was found.
Procedure: Check the data entered.
Solution: There can be several reasons to this error and the most common error that I do is not releasing the BOM.
T-code – CS02 - Click on header Change BOM status to “1”
Tuesday, December 15, 2009
Invoice number range skipping
1. Number range object is buffered. Please refer to note 62077 for details.
2. Update terminate/short dump occurs while billing document update.- the number is set in to the invoice at the beginning of the program If an interruption of the process happens after the assignation of this number, the number has run in the range and cannot be recovered. Update terminations in transaction VF01 and VF04. The billing document number is reserved prior to the update. After a possible update termination, it cannot be used again. Update terminations are displayed in transaction SM13. At present, there is no possible solution.
3. Incorrect user exit, eg. in Program RV60AFZZ, USEREXIT_NUMBER_RANGE.
Please check the following notes in order to solve this incidence: 175047 Causes for FI document number gaps (RF_BELEG) 19050 Gaps in document number sequence for billing document.
Unfortunately nothing much can be done on the missing/gaps on invoices as this problem happen randomly & not able to reproduce.
As you might need to answer to the auditor on the gap of the invoices, report RFBNUM00 from note 175047 will help you to display document number gaps to the auditor if in your country the FI document numbers must be assigned continuously. You use this report to document the number gaps and the auditor will accept it.
It is known that in different countries you have to explain document gaps to Legal Authorities. For this reason there is report RFVBER00 to document gaps occurred due to an update termination.
As already stated above report RFVBER00 does only list update terminations that are not older than 50 days (or according to what time is maintained in your system). So it could be that this log has already been cleaned up. It is necessary that these update terminations are documented before the 50 days expire.
Or a second possibility is that the gaps occurred NOT due to an update termination. Gaps without update terminations be (easily) explained. They can be (only) detected via report RFBNUM00. Report RFBNUM00 display these document number gaps for the number range object RF_BELEG.
Deleting old Support Desk messages in SAP-CRM.
is CRM_SERORD. The basis messages cannot be archived because there is no archiving object existing for them. What you can do is to set the deletion flag (status I0076) for every message you do not need any more.
Afterwards you can use report Z_DELETE_BASIC_NOTIFICATIONS provided in the attached note: #566225 Report to delete the basis notifications with deletion flag for CRM test messages alternatively the report CRM_ORDER_DELETE can be used with the following restriction.
Deleting of CRM message with report "crm_order_delete" works only if the item of the CRM message (with exists in the background without being displayed) is not released. But if you are using transactiontype SLF1
for the CRM message the status 'Released' is set for the item as soon as you set the status 'In process' for the message. As 'Completed' is a follow-up status of status 'In process' you cannot delete the CRM messages anymore using the report.
To set the deletion flag for the basic notification you have to use transaction DNOTIFWL. Here you have to set the status 'complete notificattion' so that it is set to completed. Afterwards you can set the status 'Mark for
deletion' at the same place.
Wednesday, December 9, 2009
Cross Functional
•How is output in R/3 system processed?
•What configuration enables you take different print out of invoices than in the standard output type?
•What types of free goods master records can be set up?
•What data is specified in a text access sequence?
•What data must be set up for the output type to automatically determine output?
•Give few examples of material substitutions.
Tuesday, December 8, 2009
Credit management
•At what organizational level does the Credit limit check take place?
•What is a risk category?
•What can you assign to credit control area?
•What is the relationship between company code and credit control area?
•Where can you manage currency for credit management?
•When does system carry out credit checks?
•What is the impact of credit checking on sales document if the customer is over exceeded credit limit?
Special Transactions
•Give a short description of the processes in third party business transactions.
•What item category group in the material master automatically determines the third party item category?
•Which key in sales order triggers purchase requisition from sales order?
•Which options are available for representing the movement of goods between plants within your company?
•Which special features must you take into account when transferring stock across company codes?
•What are the different ways of procuring materials for a sales order in the R/3 system?
•What is the consignment stock processing?
•Give a short description of the processes in consignment stock processing.
•If we want to ship product from plant associated with another company code what must be set up?
Customer master
•What role does the account group play for the customer master and what does it control?
•What are the most important factor for selecting fields when you maintain customer and material records?
•Give examples of standard Account group?
Availability Check
•What can you do if there are not enough available goods?
•What is requirement class used for?
LIS - Logistic Information System
•Where does the data in the SIS come from?
•What are standard analysis for?
•What is an update analysis for
•When should statistical data be restructured?
Monday, November 30, 2009
Tables in SD transactions
VBAK: Sales Document - Header Data
VBKD: Sales Document - Business Data
VBUP: Item Status
VBAP: Sales Document - Item Data
VBPA: Partners
VBFA: Document Flow
VBEP: Sales Document Schedule Line
VBAKUK: Sales Document Header and Status Data
VBUK: Header Status and Administrative Data
VBBE: Sales Requirements: Individual Records
SALES - header
VBUK: Header status and administrative data
VBAK: Sales document: Header data
VBKD: Sales document: Business Data
VAKPA: Partner index
VEDA: Contract
VBPA: Partner
VBUV: Incompletion log
VBFA: SD document flows
VMVA: Matchcodes
STXH: Texts: Header
STXL: Texts: Line
NAST: Output
JSTO: PP status
Sales activities
VBKA: Sales activity
VBUV: Incompletion log
VBPA: SD document: Partner
SADR: Address
VBFA: SD document flows
NAST: Output
STXH: Texts: Header
STXL: Texts: Lines
Logical database:
AK V: Sales documents
SD Delivery Document
LIPS: Delivery Document item data
LIKP: Delivery Document Header data
Billing Document
VBRK: Billing:Header data
VBRP: Billing:Item data
SD Shipping Unit
VEKP: Shipping unit item (Content)
VEPO: Shipping Unit Header
Delivery Due Index -
VBUP: Item status
VBAP: Sales document: Item data
VBKD: Sales document: Business Data
VEBA: Contract
VBLB: Forecast delivery schedules
VBEP: Sales document: Schedule line
VBBE: Individual requirements
VBBS: Summarized requirements
VBUV: Incompletion log
VBFA: SD document flows
VBPA: Partner
JSTO: PP status
NAST: Output
STXH: Texts: Header
STXL: Texts: Lines
KONV: Conditions
Shipping
VTTK: Shipment header
VTTP:Shipment item
VTTS:Stage in transport
VTSP:Stage in transport per shipment item
VTPA: Shipment partners
VEKP: Handling Unit - Header Table
VEPO: Packing: Handling Unit Item (Contents)
Material Master
MARA: General Material Data
MVKE: Sales Data for Material
MARC: Plant Data for Material
MARD:Storage Location Data for Material
MAKT:Short texts
MARM: Conversion factors
MLAN: Sales data (for each country)
MAEX: Export licenses
MBEW:Valuation data
MLGN: Warehouse management inventory data
MLGT: Warehouse management inventory type data
MVER: Consumption data
MAPR: Pointers for forecast data
MCH1:Cross-plant batches
MCHA: Batches
MCHB: Batch stocks
KNMTK: Header table
KNMT: Data table
Bill of Material (BOM)
MAST: Material assignment to BOM
EQST: Equipment assignment to BOM
KDST: Sales order assignment to BOM
DOST: Document assignment to BOM
STST: Standard object assignment to BOM
TPST: Functional location assignment to BOM
STKO: BOM header data
STZU: Time-independent STL data
STAS: BOM item selection
STPO: BOM item data
STPU: BOM sub-item data
Logical databank for material master
CKM: Material master
MSM: Material master
Customer Master
KNA1: General Data
KNB1: Customer Master (Company Code)
KNB4: Customer Payment History
KNB5: Customer master (dunning data)
KNBK: Customer Master (Bank Details)
KNBW: Customer master record (withholding tax types)
KNKA: Customer Master Credit Mgmt.
KNKK: Customer Master Credit Control Area Data (credit limits)
KNVA: Customer Master Loading Points
KNVD: Customer master record sales request form
KNVH: Customer Hierarchies
KNVI: Customer Master Tax Indicator
KNVK: Customer Master Contact Partner
KNVL: Customer Master Licenses
KNVP: Customer Master Partner Functions
KNVS: Customer Master Shipping Data
KNVT: Customer Master Record Texts for Sales
KNVV: Customer Master Sales Data
KLPA: Customer/Vendor Link
Pricing
KONH: Conditions header
KONP: Conditions items
KONV: Procedure ( billing doc or sales order)
KOND: contracts
VEDA: Contract data
KOMK: Pricing Communications-Header - Structure
KOMP: Pricing Communication Item - Structure
Output
NAST: Message Status
Use of Class Characteristics in QM
One of the most Critical Requirements I have came across is, Transferring Specification Values from Engineering Specification to Inspection Specification without User Interaction. I am Explaining this Requirement in brief below,
Engineering Department is Responsible for Designing Specification for Finished Product and Quality Management will Carry out Testing Accordingly, But in most of the Industries This is Paper based Engineering department will write down there Specification values for each parameter on a Specification format after approval this Specification format is transferred to Quality department now QM job is to copy those specification onto there Inspection Specification format.
Here if Quality engineer makes mistake while copying then it leads to erroneous results. To avoid this user mistakes as soon as Engineering Department maintains Specification System should take care of transferring this Specification to Inspection Specification without user interaction.
We achieve this by using Class characteristics and its linkage with Inspection Characteristics in Material Specification. Detail step by step Procedure is as follows,
Step 1: Create Each Engineering Specification Parameter as Class Characteristic in SAP.
Class Characteristics:
Here Class Characteristic means Specification Parameter which is required to be tested / Inspected During Quality Check.
Step 2: Create Batch Class.
Sunday, November 29, 2009
Plant specific number range at Invoicing
Step-1:
Create different number range Interval:-
T-code - SNRO; Use Object RV_BELEG. Click on number Ranges - Click in Change view (Pencil Marked) of Interval.
Add new interval.
Tips: Since, Its a plant specific number range you might want to use Common Starting Alphabet for each of your plant to make your life easier.
Step-2:
T-code: SE38, Use Userexit - RV60AFZZ
Use code below.
data : lt_xvbrp like xvbrp occurs 0,
ls_xvbrp like line of xvbrp.
data : lv_werks type werks_d.
data : lv_count type i,
lv_numki type numki.
data : lt_xvbrk like xvbrk occurs 0,
ls_xvbrk like line of xvbrk.
data : lv_flag_exp type i value 0,
lv_flag_dom type i value 0.
types : begin of ty_vbak,
vbeln type vbeln_va,
end of ty_vbak.
data : lt_vbak type table of ty_vbak,
ls_vbak type ty_vbak.
If xvbrp is not initial.
lt_xvbrp[] = xvbrp[].
sort lt_xvbrp by werks.
delete ADJACENT DUPLICATES FROM lt_xvbrp COMPARING werks.
describe table lt_xvbrp lines lv_count.
if lv_count gt 1.
message e398(00) with 'Different Plants for Single Billing Not Possible'.
clear lv_count.
elseif lv_count eq 1 .
if lt_xvbrp is not initial.
if sy-tcode ne 'VF11'.
read table xvbrk into ls_xvbrk index 1.
ELSE.
read table xvbrk into ls_xvbrk WITH KEY VBTYP = 'N'.
ENDIF.
if sy-subrc eq 0.
if ls_xvbrk-fkart ne 'ZEXP'.
read table lt_xvbrp into ls_xvbrp index 1.
if sy-subrc eq 0.
select single numki from zsd_binr into lv_numki
where werks = ls_xvbrp-werks
and fkart = ls_xvbrk-fkart.
endif.
endif.
endif.
endif.
if lv_numki is not initial.
US_RANGE_INTERN = lv_numki.
else.
message e398(00) with 'Number range not Maintained for' ls_xvbrp-werks.
endif.
Friday, November 27, 2009
Product Hierarchy
Note: In my case I am taking 9 levels and each levels with 2 digits. Remember !!! I cannot go beyond 18 Digits total no matter how many levels I have so Mathematically, you can have maximum of 18 levels.
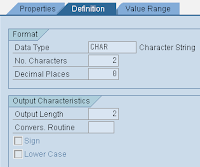
Education Cess not calculated
Why?? well this is one the SAP's old code but you dont really have to bother as long as you has the solution :)
Tax on Goods Movements-India-Basic Settings-Determination of Excise Duty-Condition-Based Excise Determination-Classify Condition Types.
Procedure Condition Type Condition Name
JINFAC Z (custome Condition Type) AT1ARPERC A/R AT1 Percentage
Export from India to Nepal & bhutan
Tcode - SE37.
Apply code:
if SH_REGION = 'NP' or SH_REGION = 'BT'.
E_CUST_TYP = 'L'.
E_T_LOCEXP = 'NEPAL'.
E_EXP_TYPE = ' '.
Endif.
Note: Remember in case code ablove I am assuming BT is Bhutan and NP is Nepal. If in your case its not the case then you have to declare the Country codes for Nepal and Bhutan.
Wednesday, November 25, 2009
Warranties configuration
In my previous post I have explained you about how warranty is linked with serial number and equipment and how to configure serial number for automatic creation of equipment and make it a mandatory field at delivery etc.
In this post you will learn to verify warranty validity, add warranty view in equipment master, add data management field to Equipment master etc.
Activating Warranty in Customer Services to Check Warranty Validty.

Plant Maintenance and Customer Service- Master Data in Plant Maintenance and Customer Service - Basic Settings – Warranties - Define Warranty Types.
Monday, November 23, 2009
Serial number for Equipment Warranty / Material Warranty / Warranty given on sold product.
This section will deal with how to assign warranty to material sold. Normally, discreet manufacturing industry gives warranty validity from the date of delivery. So I am giving you configuration detail of assigning warranty at the time of delivery.
Theory: a warranty is given on a equipment and equipment is assigned to every serial number. In a nut shell every material sold having a serial number can have a warranty and any material that does not have serial number cannot not have warranty.
Equipment is unique to each serial number + material. Ths configuration deals only with serial number profile and automatic creation of equipment assigned to a serial number. This configuration will also help you to assign validity date to warranty.
T-code- OIS2.

Note: This activity can be done even thru IE06 or IQ09.
Double click on check box below ‘Eqpt’
Input Warranty begin and end date. Save.
Now the biggest question is when you get the material back how you check the warranty.
There are few configuration that you can do in CS – Customer services to make sure the warranty check happens. I will post the configuration very soon.
Serial number profile
Firstly, create serial number profile for sale order, Profile will allow you to assign serial number at sales order level.
Saturday, November 21, 2009
Calcutta
Friday, November 20, 2009
Bangalore
